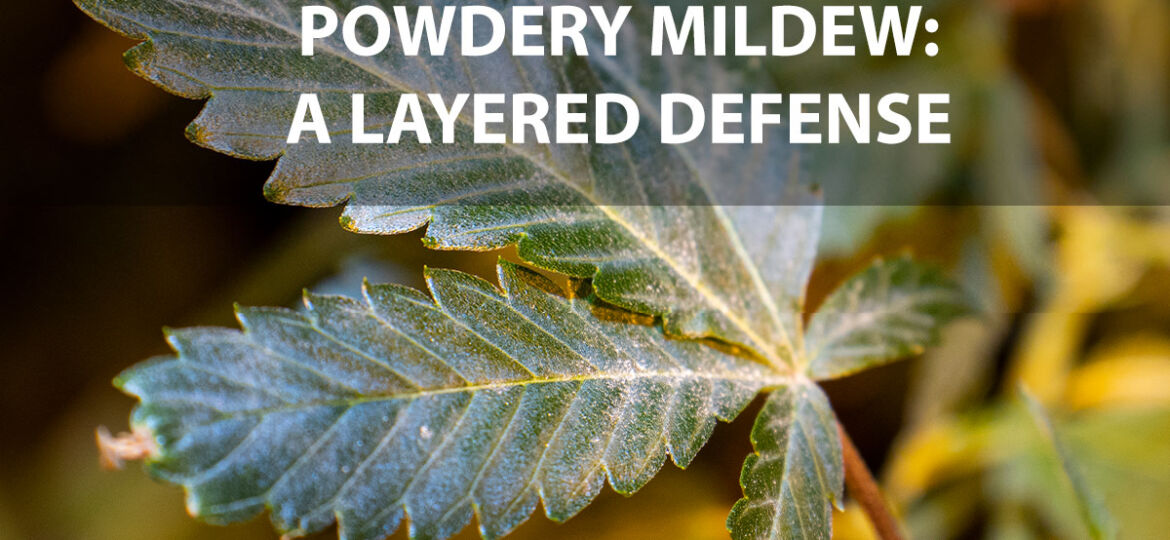
Powdery Mildew: A Layered Defense
There is no silver bullet to guarantee a contamination free indoor grow, especially with human error at play. However, Integrated Pest Management (IPM) offers a layered approach that focuses on long-term prevention of pests and microorganisms. It is all about the details, the macro aspects of contamination management. Prevention is the focus of IPM and the strongest approach you can take against common contaminants such as powdery mildew and botrytis.
Having a robust IPM approach will equip you with a hardy, layered defense. Here is what IPM entails:
Observation
Observation is an important place to start in any indoor growing environment. Controlling pests without harming employees and the environment around you should be the priority. Vigilant observation is key to accomplishing this. First, identify issues you are currently dealing with. Next identify issues that may come up in the future. Learn the signs and symptoms of microbial diseases and pest infestations. This will help you develop and employ best practices and an efficient workflow for a successful IPM plan.
Observation should technically start before any crop is brought into your grow space. Make sure the space is clean and sanitized, has good water drainage, and any repairs have been completed. Were there previous pest issues in the space? Were previous treatments applied in that space? If you’re using soil, did you put it under a microscope to check for mites or other pests?
Observation also includes thorough inspection of incoming plants. Utilize the knowledge you have developed about the signs and symptoms of diseases and pests to double check your plants. Whether or not there are any signs, it is standard procedure to quarantine new plants. During quarantine, it is recommended to treat plants with several applications of UVC disinfection. UVC cripples the development and spread of things like powdery mildew, which can be on a plant for up to seven days before it is visible to the naked eye.
Helpful observation practices:
- Regularly and closely examine plants and soil.
- Identify and document all pests and pathogens.
- Divide the grow space into a grid to make tracking, surveillance and recording data easier.
- Use monitoring devices such as:
- Sticky traps to help you monitor insect presence and population
- Air quality and environmental monitoring to help you not only track particulate levels, but also alert you to any changes in conditions (such as spikes in certain sized particulates, increases in humidity or temperature, and more).
- Determine/define thresholds for contaminant levels.
- Establish checklists for assessments to be made and when.
- Devise charts that correlate with your checklists and are easy to fill out while doing assessments.
Cultural and Environmental Controls
A well-designed indoor grow will make it easy to limit exposure to contaminants. No matter the design, solid cultural practices can be employed to prevent pathogens from entering your indoor grow spaces. In the event that your grow is exposed to contaminants, indoor environmental controls can inhibit pathogen propagation. Powdery mildew and botrytis are encouraged by humidity. Adequate fans and ventilation filtration are essential.
Helpful cultural and environmental practices:
- Have specific spaces in the facility dedicated to the disinfection of tools and changing of clothes/cloth covers between cultivation rooms.
- Provide a system to sanitize shoes and change gloves prior to moving from one cultivation room to another.
- Prohibit employees from wearing street clothes and shoes inside cultivation rooms.
- Implement an irrigation schedule to avoid root diseases.
- Diligently manage temperature and humidity (or more importantly, Vapor Pressure Deficit).
- Provide consistent and balanced airflow across the plant canopy.
- Install and maintain air filtration systems and regular room air turnover protocols.
Mechanical Management
Mechanical management holds great potential for contamination risk reduction. By mechanical, we mean both physical (by hand) and employing the use of non-chemical tools. This is an important partner with observation and generally the most straightforward way to deal with contamination, especially if it is still small scale. USDA researchers have found that treatment once or twice a week with UVC light followed by a four-hour dark period can help control and mitigate powdery mildew.
Mechanical management can be time consuming, but if implemented conscientiously and supported by solid observation protocols, it can help you minimize the use of chemicals and other things that can disrupt the grow environment (and increase risk to employee well-being) and company overhead.
Helpful mechanical management practices:
- Isolate and quarantine any plants showing plant disease.
- Remove any dead/dying plant matter.
- Sanitize all tools and equipment regularly, especially in between use in different grow spaces.
- Sanitize spaces and equipment between grow cycles.
- Germicidal UVC light is an excellent, chemical free approach to sanitation.
- Adopt spot treatment or routine treatments of UVC light for the prevention of outbreak and/or slowing the spread of an outbreak.
Chemical Management
Prevention is the emphasis of IPM. Pesticides and fungicides should be considered a last resort
and used in moderation. Protecting your people, the environment and product quality should be top priorities. For cannabis, minimum-risk pesticides are required (refer to pest management agencies in your state for a list of approved pesticides).
Helpful practices for when chemical mitigation is required:
- Equip employees with proper personal protective equipment (PPE) for anybody handling, mixing, applying or in range of exposure (i.e. going into space after spraying) to chemicals.
- Ensure staff is well educated about chemical use requirements/limitations and they are properly certified to use them.
- Ensure all chemical is compliant with your state’s list of approved pesticides/fungicides.
Documentation
Documentation starts in the observation phase. It is crucial for providing your grow operation the information it needs to track and learn from contamination risk. Being able to spot patterns in outbreaks will enhance your ability to mitigate them in the future. Documenting what works and what doesn’t helps continue to improve your IPM approach and grow efficiency – and in the long run, a better bottom line. It is also important for regulatory reporting purposes.
Helpful documentation practices:
- Install a few high quality data logging temperature and humidity sensors in each room and download this data after every complete grow cycle (from vegetation to harvest).
- This will help you identify if the room is within temperature/humidity specifications during all times and allows you to do a historical cross-check to see if there were any contamination problems due to inadequate mechanical HVAC equipment.
- Establish a well labeled grid system in each room.
- For example, a square or rectangular table can be one grid unit. Track if/when contamination occurs in each grid unit and how it spreads. Document how you treated this area. You might learn that one area needs better airflow when comparing similar grow cycles.
- Take samples from each bag of soil (if you’re using soil) and observe under a microscope.
- This will help you prevent using soil that comes with live pests.
- Document the soil brand and lot number, if available.
- If a bag has pests, remove it immediately from the facility, assume all bags from the same brand/lot are contaminated and return them to where they were purchased.
- Document all chemicals applied to the crops, when and where. Include irrigation and fertigation system dosing parameters and cycle timing for the duration of the crop cycle.
How Puren Solutions Can Strengthen Your IPM Plan
Puren Solutions believes in the power of layered approaches. By layering all these practices together, you will have the greatest success managing and maintaining a clean grow that produces safe, quality consumables. Helping you accomplish this is what drives us to design high quality equipment. Boost your management of powdery mildew and other contamination with industrial strength air filtration, high tech monitoring systems and germicidal UVC. Learn more at www.purensolutions.com.