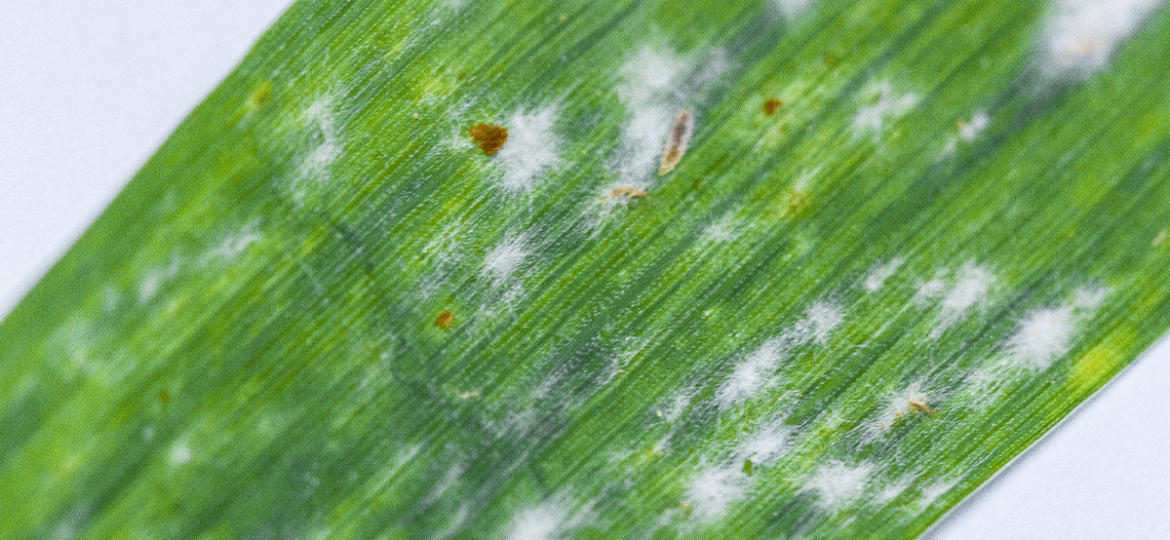
Powdery mildew is a fungal disease affecting a wide range of plants. It is one of the most common and costly diseases for nursery plants such as flowers, vegetables, and woody plants. It infects plants under a wide range of conditions. It is a challenge to prevent and mitigate. Temperature, relative humidity, light, and air circulation are all prominent factors influencing powdery mildew prevalence.
When powdery mildew is active on plants, it leaches away their nutrients. This makes the plant weaker and bloom less, ultimately reducing yields. Powdery mildew prevention is the best approach to protecting your plants, products and bottom line.
Integrated Pest Management
Integrated Pest Management (IPM) as a concept was first developed in the late 1950s. It came out of concern for the environmental impacts of the heavy and widespread use of pesticides. IPM is a layered, ecosystem-based approach focusing on the long-term prevention of pests through: biological controls, physical habitat management, modification of cultural practices, the use of chemical controls (more often though, it seeks to employ alternatives to synthetic chemicals), and the use of resistant plant varieties. IPM is all about taking action before issues arise to keep pests and contaminants from becoming a problem.
Proactive Rather Than Reactive
Monitoring is one of the most important preventative measure of IPM. It provides information specific to a current grow that inform a growers decisions. It is also key for early detection. Routinely scouting plants is essential to a structured crop inspection program. Examine the upper and lower leaf surfaces, note any irregularities and colorations, and document everything to better detect any future changes.
Culture controls include sanitation, weed control, environmental factors such as light/temp/humidity, and the use of powdery mildew resistant plants. Cleanliness alone will not guarantee pest and disease problems from happening. But it is a foundational piece of IPM that makes all other prevention methods even stronger. Common cultural control approaches include:
- Remove dead/dying plant matter. Get rid of crop residues. Wash and disinfect all tools and equipment. These habits are important for good sanitation. Clean room principles will dramatically bolster your IPM plan. We discuss this in greater detail further down this article.
- Remove all weeds from inside your greenhouse (or indoor growing environment) and from the areas immediately outside. This reduces pest habitat.
- Manage temperature and humidity (or more importantly, vapor pressure deficit ). This is an important prevention and control tool for powdery mildew.
- Maintain good drainage. Avoid standing water. This is often overlooked but important. Even if a grow space is not currently being used, keep it clean and sanitized.
Choose to grow plants with genetic resistance to powdery mildew and other pests/contaminants. This gives you a leg up in prevention and management of infections. Biocontrols (using living organisms to combat pests) will also bolster IPM, especially in light of increased pesticide resistance in many organisms.
A Shift in the Paradigm
The human eye can detect object about 4 microns (0.1 mm) in size unaided. Powdery mildew spores are between 1 to 3 microns. Powdery mildew spores spreading through a room are largely undetectable using non-sensor based monitoring systems. When you create a clean environment, you help prevent powdery mildew from taking hold. Likewise, when you fight an outbreak, a clean environment will help mitigate the population and slow the spread of active powdery mildew spores.
At Puren Solutions, we support a paradigm shift in the establishment of clean grow environments and current IPM strategies. IPM is about controls and preventative measures. These are especially important when it comes to Good Manufacturing Practice guidelines. However, the current foundation exists around these individual measures acting in lieu of or in parallel with one another to ensure a safe grow. We propose these processes be layered. First establish a foundation based on clean rooms and clean room techniques. Build IPM practices on top of this core foundation.
Puren Solutions products meet the requirements of GMP facilities. They support a solid foundation. One that in less than an hour from setup, creates an actively clean and monitored facility. This cost effective change refocuses growers time and energy. It establishes a baseline for proper plant health leading to an increase in yields, a reduction in chemical applications, and a minimization of crop risk.
Cleanroom principals bring airlocks, air showers and full body suits to mind. These tactics benefit any indoor growing environment. They are vital in some scenarios. But they are also not required for indoor growing. A cleanroom is simply defined as a “room with a defined concentration of airborne particles, designed and used in a way that the number of particles introduced into the room or originating and being deposited in the room is as small as possible, and in which other cleanliness-relevant parameters such as temperature, humidity and pressure can be controlled as required.” (VDI 2083-1) The foundations of a cleanroom are air filtration and air circulation. Incoming air is filtered and rooms maintain constant airflow. This pushes air towards filters that continuously scrub the air of contaminants.
Air Filtration and Circulation
To create a clean room you must have the entire volume of air scrubbed through a high quality air filtration system once every 10 minutes. The filters must be capable of capturing small contaminant sizes. Clean air is typically directed from the top of the plant canopy down to the floor. This will decrease the spread of powdery mildew spores and slow the spread of contamination. It is a top-down method of moving air that helps maintain even plant temperature from the top of the canopy to the root structure.
When contamination occurs, standard practice is to empty the room after harvest and sanitize all surfaces. This includes ALL parts of equipment exposed. Some large-scale growers fumigate the room with chlorine dioxide gas. This provides near 100% effectiveness to sanitize the air and all surfaces. It is an extremely effective and low labor approach to sanitize surfaces. It also has drawbacks. These include a substantial reentry delay for personnel because of extremely hazardous chemical exposure. It takes at least a full day or more before chlorine dioxide gas reaches safe thresholds for reentry. Facilities and equipment are constructed of many different materials. Chlorine dioxide will not harm stainless steel and electronics, but may degrade and shorten the life of some types of equipment.
To shorten room turnover when using chlorine dioxide, use filtration with activated carbon filters that you can remotely engage after the recommended exposure time is reached. An active air filtration system – such as the variety of option available in the E-Series air filtration units – will cut the reentry time by more than half if using new filters.
Beyond Powdery Mildew
The American Society of Heating, Refrigerating and Air-Conditioning Engineers (ASHRAE) confirms that porous media particle filtration systems (mechanical filters)remain the only systems proven to provide significant health benefits. It is crucial for the health and viability of your crops to maintain a clean grow and processing environment. It is also important for the health of your customers and employees.
Air filtration is a foundational step to establish a strong IPM foundation. When you adopt cleanroom principles and technology, your crops thrive and benefits abound for those who work with and consume what you grow. It will put you a step ahead for meeting regulation standards currently enforced as well as those to come.
The Golden Rules for a Clean Facility
- Don’t let contaminants into your facility.
- If contaminants enter the facility, control where they go and how they are captured.
- Clean facility design is a niche engineering trade that focuses on the creation of clean zones. A person or product moves from the dirty exterior through isolation zones before they enter the cleanest growing or processing zones. Each zone is cleaner and more positively pressurized than the previous zone. This pushes contaminants away from the cleanest grow room or processing center.
Learn More – Defend with Prevention
Within 30 minutes of runtime, the E-Series Air Filtration Units scrub a 2,000 sq. ft. room of 98% of all powdery mildew and contaminants 0.3 microns or larger. The Puren Solutions suite of products empower users to instantly create and indefinitely maintain clean environments. Devices that rely on photocatalytic oxidation rapidly degrade, require replacement, and are quickly rendered less effective via the buildup of dirt and dust. The levels of hydrogen peroxide emitted via Ionic Oxidation devices that periodically mist spaces are not at a level that provides sufficient or even moderate sanitation results. The Puren Solutions air filtration and monitoring units capture and retain airborne contaminants. They can then be washed and sterilized inside and out. You can use these products with complete confidence that they are not a source for spreading disease.
Units equipped with E-Guardian Monitoring measure particles 0.3 to 40 microns in size. The early warning system alerts you to increases in particle counts. You can act quickly to contain contamination outbreaks and find the source. They are IIoT-based systems so you can monitor and remotely control them from anywhere you have an internet connection. Export data to inform processes and meet regulatory reporting requirements.
Contact us today to learn more about how E-Series air filtration units are a foundational first line of defense in your integrated pest management plan.